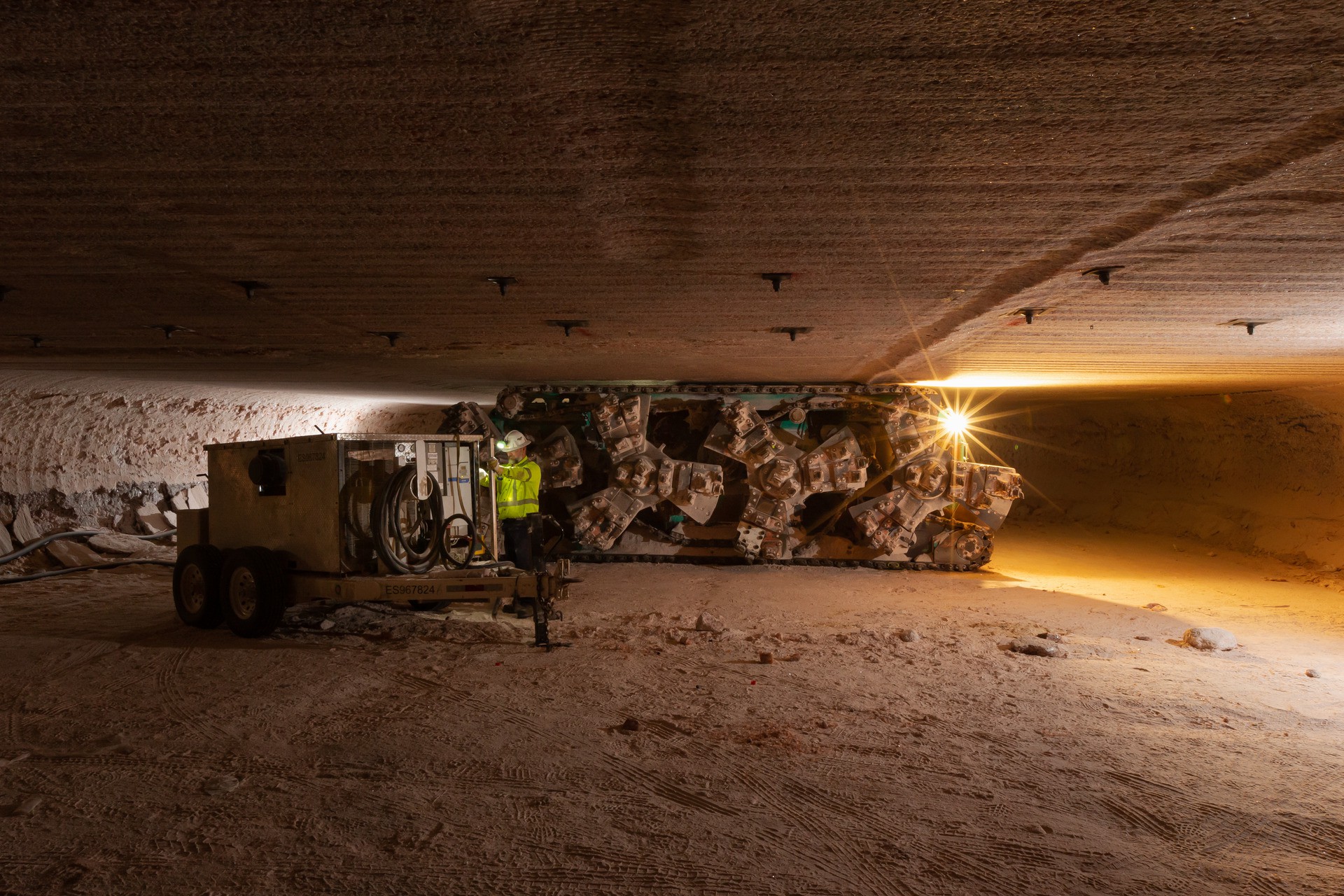
The Mosaic Company's Flagship Potash Operation in Esterhazy is Now the World's Largest
After a decade long journey and nearly $3 billion invested, Mosaic’s expansion project in Esterhazy, Saskatchewan is complete. The massive mining complex now holds the title of the world’s largest potash operation after externally verified results confirmed it can produce 7.8 million tonnes of potash.
The project was first announced in 2009, followed by shaft sinking in 2011. By early 2017, the first ore was uncovered. Two massive headframes were constructed to house powerful hoists and skips that bring the valuable ore to the surface. Construction was completed on a conveyance system to transport the raw ore to Mosaic’s two mills that sat next to the original K1 and K2 mine shafts. As surface infrastructure took shape, while underground, new mining machines fabricated in Saskatchewan were expertly assembled using a modular approach – meaning they could be partially put together above ground then carefully lowered down the shaft to save shop time and get them into production faster.
“At the time, this project was the first of its kind in the province in nearly half a century,” says Dustin Maksymchuk, Esterhazy’s General Manager. “It began during a market up-swing, but with the time it takes to build a new potash mine, much of the work was completed during depressed markets and a global pandemic. We accelerated our timeline several times and delivered the project well ahead of the original timeline and on-budget. This project is a true testament to our team’s persistence and endurance. This is a 50 plus-year investment for the company – and a generational commitment to Esterhazy and Saskatchewan.”
K3 came fully online in 2022, and its design and technology make Mosaic’s Esterhazy facility the world’s most advanced and largest potash operation. The early development of K3 started in 2009, with the sinking of the shaft beginning in 2011, and crews successfully reaching ore level in 2017. The cost to build K3 was $2.9 billion. |
Mosaic added 13 automated mining machines, often called “miners” to its underground fleet, which cut through ore beds left behind in the Cretaous period. The automated miners are controlled by professional operators housed in the new Integrated Operations Centre (IOC).
The IOC system is constantly evolving with feedback from employees operating the system and those working underground. |
Innovation and Technology Power Mosaic’s Esterhazy Complex
Esterhazy’s new IOC uses the latest technology in cameras and sensors to monitor and operate the mining machines and the conveyance system that moves potash to surface and then over 11 kilometers of enclosed conveyors to reach one of two mills for processing.
“The IOC streamlines the flow of information and optimizes our operation from end-to-end,” says Dustin. “It’s revolutionized how we work, and that’s a good thing. This is the future of mining – it offers improved safety and empowers our people to make the best decisions faster and with real-time information.”
Today, the underground footprint of K3 is about four times the size of the City of Yorkton. By 2025, the mine will be double the size of the City of Regina. What is more incredible? Wi-Fi is also accessible throughout the entire underground to power the extensive digital footprint. |
Owning the Ground
Automation has improved safety for employees because they can monitor most aspects of the operation from a safe distance, while also increasing productivity with 24/7 run-time.
Mining at K3 is 150 to 300 feet deeper than Mosaic’s previous two underground mines, which impacts what is called ground conditions by the industry. Underground personnel must be always aware of the conditions above their hard hats and below their work boots.
Mosaic introduced a specialized “Own Your Ground” program to make ground condition checks top of mind on every shift.
“Safety is at the forefront of every decision we made when building every part of this project,” says Kelly Strong, Vice President, Mining, North America. “The team was intentional with its design and when transitioning our workforce into a new environment. You must adapt your processes and policies to fit a modernized underground operation with different conditions.”
Thirteen automated miners complete the underground fleet at K3. The 13th miner officially joined the fleet in July 2023. |
Esterhazy Keeps on Crushin’ It
Crushin’ It became the slogan for Esterhazy as the team ramped up production to prove its new operational capabilities.
Today, strategic investments are underway in the K1 and K2 mills to relieve operational bottle necks and provide even more product flexibility.
“K3 has been Mosaic and Esterhazy’s future for the past decade -- and I’m proud to say the future is finally here,” says Dustin. “This is a rural community in Saskatchewan, that’s now home to the largest potash operation in the world. That’s huge for us, and it’s a big deal for the local area and the entire province."
“The magnitude of this project is hard to truly comprehend. As a company, our mission is to help the world grow the food it needs," says Kelly. "We take that responsibility seriously. The world is counting on us every day, and now we’re ready to deliver 50 more years of potash from the world’s best reserves to farmer’s fields so they can grow food that feeds us all. What an incredible story for us to tell.”