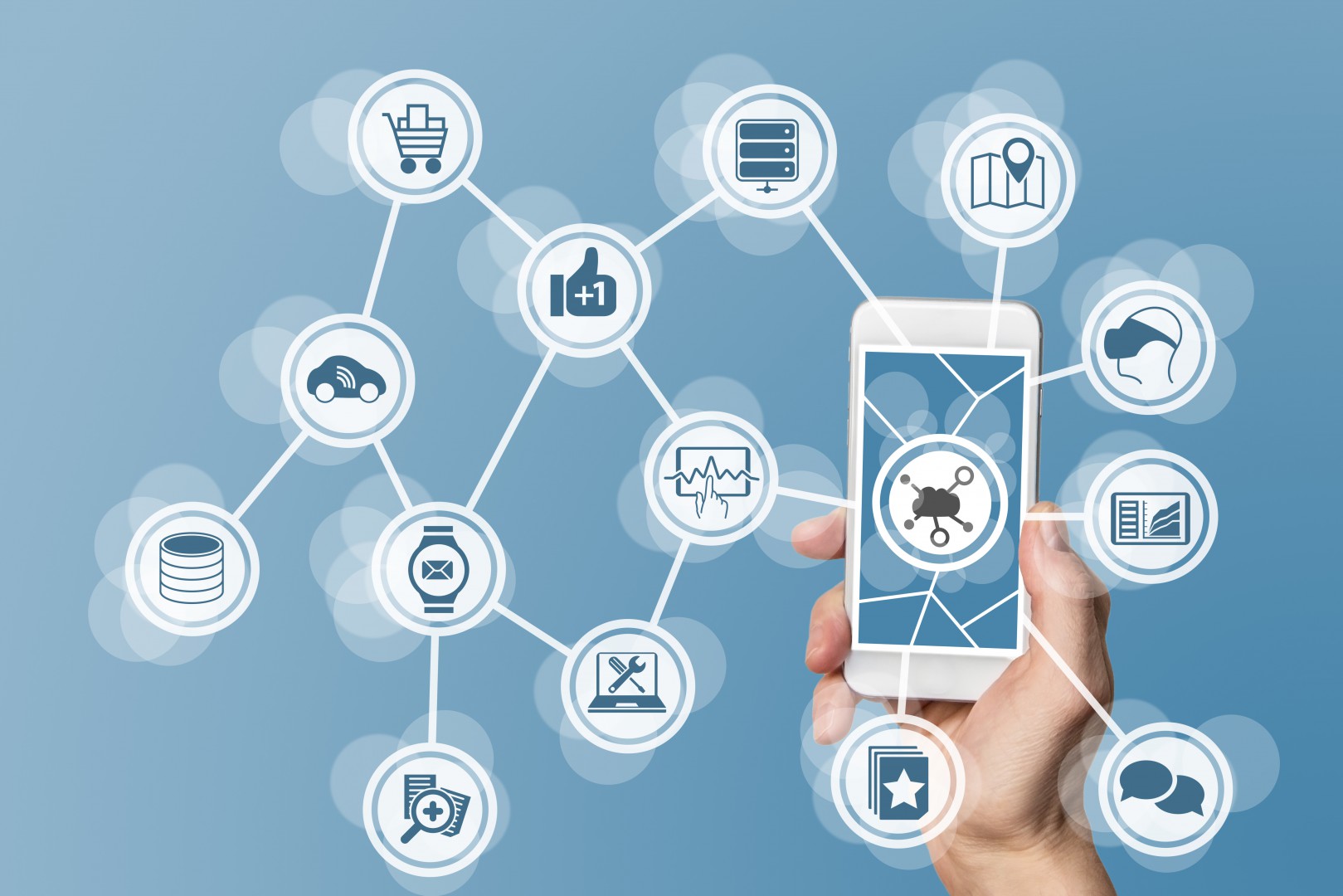
Our Innovation Journey: Improving Employee and Customer Experiences through Digitization
How much business would Google lose if search results weren’t returned immediately? How much business would Amazon miss out on if customers didn’t know when their order would arrive? Like other companies around the globe, Mosaic is focused on using technology to improve and create seamless experiences for both employees and customers. Many of those changes are being made through digitization – converting text, pictures or sound into a digital form that can be processed by computers.
“Digitization is basically converting cumbersome, manual processes – where information is hard to retrieve and use – to simple, efficient processes where the data is readily accessible anytime, anywhere," explains Chris Hagemo, Sr. Director, Digital Strategy – North America. At Mosaic, that could be as simple as switching from paper to electronic invoices or as complex as improving our customers’ buying experience.
“This area of our digital strategy can be difficult to tie hard-dollar savings to, but the impacts are real, and it will have a pronounced effect on the daily experience of our employees and customers,” says Chris. “And employees aren’t just spectators or recipients of this change, they're co-creators helping make it happen.”
Microsoft’s PowerApps and other digital tools are enabling our employees to create mobile applications and use analytics to improve their own processes. With a little training, employees are using, sharing and learning from valuable real-time data collected through mobile applications they build themselves.
“300 in 3” Mobile Application
We’re using technology in new ways across our North America Business to help keep people safe. One example is through use of
mobile applications, including the new “300 in 3” PowerApp being used by employees and contractors to proactively identify and
address potential risks on our Esterhazy K3 and other capital projects. Watch this video to learn more.
The new “300 in 3” PowerApp was developed by a
group of employees who wanted to find an assessible,
efficient way to engage empoyees and contractors in
reducing safety risks on capital projects.
To kick off National Safety Month, we want to spotlight one of 50 PowerApps currently in use across our North America Business – the new “300 in 3” mobile application, which is helping us reduce safety risks on our Esterhazy K3 and other capital projects.
Developed by a group of employees to engage workers in proactively identifying and addressing risks, the application makes it easy for employees and contract partners to quickly and efficiently complete safety observations in the field – either directly through the application or an online form. The goal is to complete 300 safety observations every three days across all capital projects.
Microsoft’s PowerBI, an analytics solution that can be embedded in any PowerApp, is then used to analyze and share real-time insights from data collected through those observations.
“Before this application, safety observations for capital projects were captured on paper forms or through another application that was not easily assessible by our many contract partners,” explained Geoffrey Flury, Vice President, Capital – North America Business. “Now – not only has ease of access and use of the application led to a significant increase in the number of safety observations completed – we have access to real-time data that allows us to identify trends or indicators, and where warranted, put corrective measures in place to keep our people safe.”
Capturing outcomes and actions is an important part of the
safety observation process. The “300 in 3” mobile application
allows us to track corrective actions and those requiring
additional follow-up in real-time, which is especially
important for observations that could have resulted in an
injury or incident. Also important, it allows us to recognize
and easily share positive findings and best practices across our
operations.