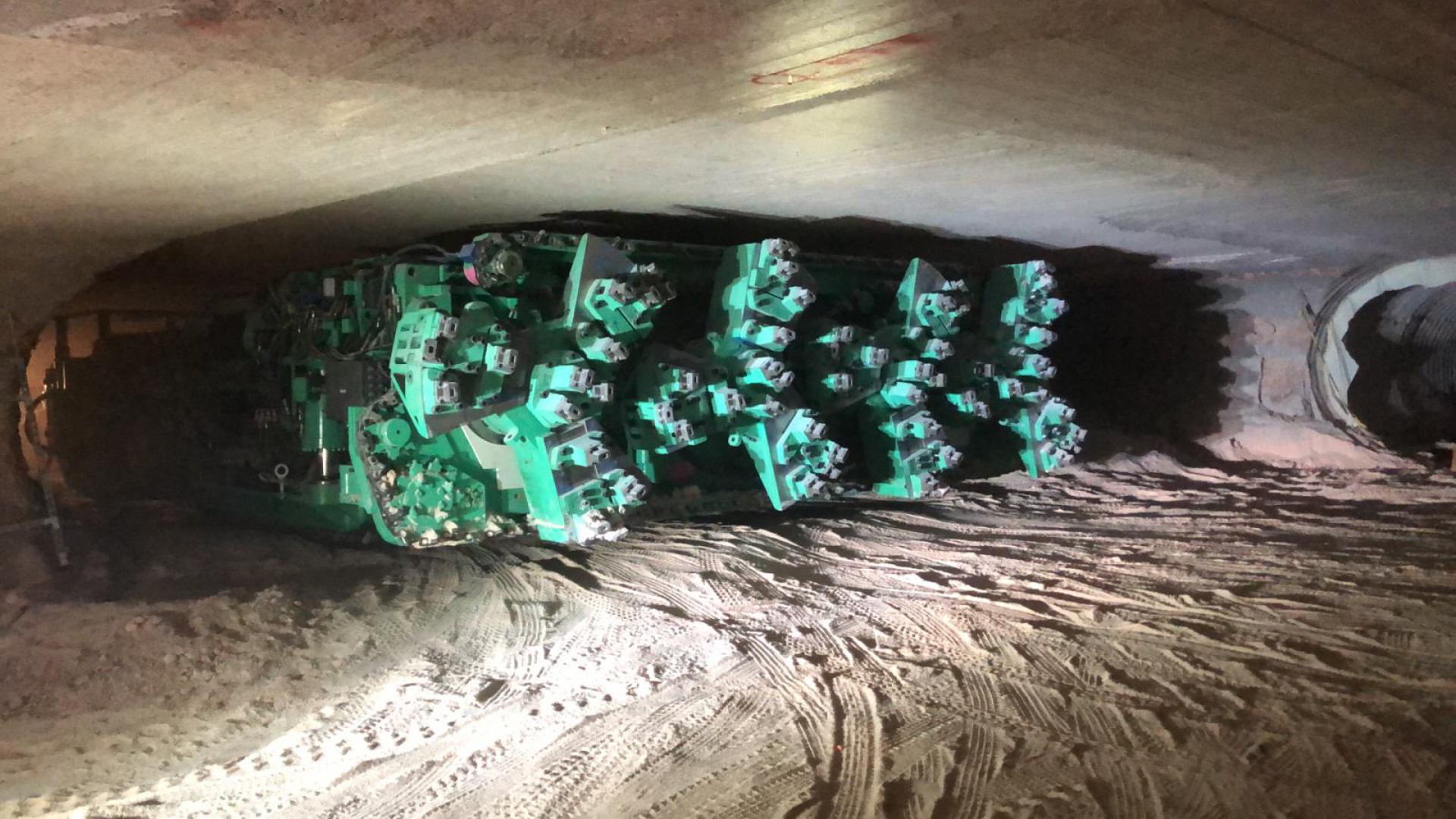
NEXTGEN: Esterhazy Team Surpasses One Million Tons Mined in First-Pass Automation
Mining machines at Esterhazy K3 are now mining autonomously in all three “passes” they make to mine an area. In March, the Esterhazy team surpassed an impressive milestone – mining one million tons in first-pass automation. On the first pass, the machines set the direction and forge a new path through rock while another automated machine follows behind them installing hardware to build a conveyor belt. Watch Esterhazy K3’s automated mining machines in action. |
After years of collaboration, development, testing – learning from trial and error along the way – the Esterhazy team is now successfully running K3’s mining machines autonomously in all three “passes” they make to mine an area. The team began testing first-pass automation in April 2021 at K3, and they surpassed an impressive milestone in March – mining one million tons in first-pass automation. Six of the ten machines in K3’s fleet can operate autonomously on the first pass, and all have been operating autonomously on the second and third “side” passes.
Running these machines with minimal human intervention reduces risk for our employees and eliminates downtime, as they can safely operate 24/7. Automation allows employees who previously worked in close proximity with mining machines to operate and monitor them from a distance – providing better, safer working conditions for employees, while also providing an opportunity to increase production.
“Two of our main goals when we formed Esterhazy’s automation team in 2015 were to automate the steering of our mining machines in first pass and build the conveyor belt automatically,” explains Anthony Sparvier, K3 Automation Superintendent. “We’ve accomplished both those goals, but there were significant challenges to overcome along the way.”
Esterhazy’s automation team worked closely with third-party experts throughout design and development – performing extensive tests to confirm the accuracy and reliability of various systems. They also worked with Esterhazy’s geologist to confirm autonomous mining would not have any geological impacts.
Building operators’ confidence and trust in autonomous operations took some time. “The same control aspects were in place, but the newer mining machines and the Human-Machine Interface (HMI) screens were quite a bit different than what our people were used to,” explains Sparvier. “All our operators mine differently but our mining algorithm mines the same regardless of who is at the machine, so there was also some confusion and misunderstanding about how the machine steers.”
Sparvier says the key to building that trust and confidence was involving the operators, transparently sharing about success and challenges along the way, and providing training. “We developed a training presentation with all of the operators from each crew who were at the mining machine when we were initially testing first-pass automation,” says Sparvier. “The training goes over the method, algorithm and what to expect with cutting in automation. It also provided answers to some of the typical questions we were getting about steering.”
There are still some challenges to overcome, but the Esterhazy team is excited about the progress they are making. “We couldn’t have accomplished all we have without support from all levels of our organization – from our operators to senior leaders,” says Sparvier. “It truly has been a team effort, and we’re not done yet. We still have more training to do, and more projects are on the way to make our automation program more robust, reliable and intuitive.”
Mining machines make three “passes” when mining an area. On the first pass, they set the direction and forge a new path through rock while another automated machine follows behind them installing hardware to build a conveyer belt. During the second and third passes, the machines follow the path of the conveyer belt to mine ore—first on one side of the belt, then the other. The control center on the surface being designed as Esterhazy’s Integrated Operations Center is equipped with communications and cameras that employees use to monitor progress of the machines from the surface. They can stop and start the mining machines to manage ore flow and schedule in-person checks as needed to ensure safe operation and support the mine plan.ΓÇ» |